WheelWatch
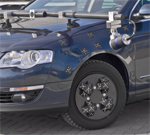
Non-contact high speed monitoring of wheel motion on a moving vehicle or in a test station
- Optical measurement system using a high-speed digital camera
- No mechanical connection between sensor and wheel
- Self-referencing to vehicle coordinate system in real time
- Easy to integrate into test stations
- Very short setup time
- Accurate measurement of all wheel parameters including track, camber inclination, spring travel, steering angle and wheel clearance
- Several wheels or axles can be monitored simultaneously
Vehicle development for optimal driving characteristics
Chassis design is very important to new car development as it ensures optimal driving characteristics. Choosing the right design parameters requires extensive testing. For example, wheel housing design must allow sufficient clearance for various types of tires and their particular movements, and each wheel must be monitored to see how it behaves under extreme driving conditions or on bad pavements. Past studies have relied on mechanical monitoring devices which are complex in handling and may influence the driving behavior.
WheelWatch provides a revolutionary approach to wheel monitoring. Due to its functional principle, it offers many advantages, facilitates wheel monitoring and delivers more exact measurement results.
High-speed camera TraceCam F
WheelWatch is built around TraceCam F which consists of a high-resolution high-speed digital camera with 1.3 million pixels, an integrated high performance flash and an image analysis processor. The integrated high-speed digital camera features extremely short shutter speeds of just a few microseconds that are necessary for long duration tests. The high quality camera also ensures the system is robust and stable over time.
It provides data at a frequency of 490Hz, ideal for studying and optimizing static and dynamic chassis parameters. Measurements are controlled automatically and may be collected over long periods of time. The triggering function ensures that multiple sensors are fully synchronized.
The camera can be mounted at a distance of less than 500mm (20 in) from the fender. The camera processor uses TCP/IP protocol to communicate with the laptop computer which controls the system. The computer is placed in the test vehicle. The vehicle 12 Volt power system provides power during the test drive.
Functional principle
For the measurement of wheel movements, one camera for each wheel is mounted so that the wheel as well as part of the surrounding fender is visible. Special optical targets applied to the fender define the vehicle coordinate system. A lightweight carbon fiber wheel adapter is fixed to the wheel.The position of the camera does not have to be stable as WheelWatch recalculates its position continuously using the reference targets on the vehicle fender. The wheel movement measurements are always provided in the vehicle coordinate system. Movements of the camera or camera mount do not influence measurement results, making the system inherently more stable than competing systems.
The driver manually triggers the beginning and end of a measurement session. No other interaction with WheelWatch is required. The high-speed camera collects wheel measurements at a rate of up to 490 times per second.
The image processor analyzes the digital images in real time and passes the measurement values to the notebook computer. Wheel target positions and target trajectories are available shortly after the image acquisition. In addition, WheelWatch computes all six degrees of freedom of the wheel in the vehicle coordinate system.
WheelWatch advantages
WheelWatch with TraceCam F has been developed in close cooperation with the automotive industry, and the system has been designed to provide the features and functionality that are most beneficial for this application.
Short setup time
A major requirement is fast and easy system setup. The TraceCam F camera is designed to be mounted quickly on the vehicle without the requirement of sophisticated tools such as tail lifts. Assembly of a four camera system, mounting frame, wheel adapters, and calibration and referencing to the vehicle coordinate system takes less than one hour. The system is ready to begin making measurements immediately after installation.
Measurement accuracy
WheelWatch measures wheel movements for a vehicle traveling at speeds of up to 250km per hour (160mph). The system is also capable of observing extreme driving maneuvers. Points are measured to an accuracy of about ±0.1mm (0.004 in) and angles to an accuracy of about ±0.015°.
Simultaneous measurement of several wheels
Several cameras may be precisely synchronized. WheelWatch may also be synchronized with other measurement devices. In this case, the cameras can either be controlled by an external synchronization signal, or they can deliver the master signal themselves for all sensors applied in the test. In addition, each individual measurement value is time stamped. Thus, the application on several wheels and with other measurement sensors is possible.
Integration into test stations
The WheelWatch system is particularly suited for integration into vehicle test stations. Data acquisition between numerous cameras over multiple axles and even with other sensor types may be precisely synchronized. WheelWatch saves the measurement data digitally, making these suitable for database storage. Data may be converted from digital to analog during tests if real time machine control is required. An optional data router allows the computer to control WheelWatch system functions via TCP/IP.
No mechanical connection between the sensor and wheel
Measurements are non-contact and require no mechanical connection to the wheel. Consequently, driving characteristics of the vehicle are not influenced by the measurement equipment and steering motion is not restricted in any way. WheelWatch completely overcomes the disadvantage of ther wheel monitoring methods because there is no risk of creating erroneous measurements due to the mechanical connection between sensor and wheel.
Low weight
No heavy analysis units, batteries or controllers that may influence driving behavior are required, and the camera mount does not need high stability. Light weight mounting components can be used, which eliminates any significant influence on driving behavior.
Further application areas
TraceCam F may also be used in related application areas such as door closure tests, engine movements, machine vision or robot control.