MoveInspect DPA
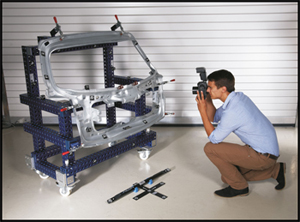
Highly-precise CMM with hand held digital camera for 3D data collection
AICON's DPA systems are portable coordinate measuring machines that use a digital camera for data collection. They are applied both for the 3D inspection of components and for 3D process analysis, for example for analyzing deformations of sheet metal and plastic parts.
The following are typical applications for DPA:
◦Deformation analysis, e.g. in crash tests
◦Inspection of sheet metal parts and tolerance analysis
◦Fixture inspection
◦Comparison with CAD
◦Measurement of large objects, e.g. steel fabricated structures
◦Roundness inspection, e.g. tunnels or tanks
Flexibility with respect to object size and and location
The DPA systems cover a wide range of application. They will measure parts from a few millimeters up to many meters in size. Objects as large as entire aircrafts can be measured. AICON's DPA systems employ a hand-held camera and are therefore particularly suitable for use on large objects that cannot be moved to a CMM and must be measured at their current location. AICON's DPA systems are also especially suitable for use when the environment requires that time on site is minimized. Moreover, they are very useful in areas where movement is restricted as they do not require stable measuring instrument positions. AICON's powerful DPA software delivers results within seconds of completion of the measurements.
Work flow
Targets or adapters are placed at all object features relevant to the inspection. There are adapters for boreholes, edges etc. as well as special adapters for measuring reference points. In addition, trim lines, punch holes etc. can be measured without any additional targeting. The targeted part is photographed with a high resolution digital camera from different directions. These photographic images are processed either simultaneously with data collection (online processing) or after data collection (offline processing) with AICON's powerful software. This software, which runs on a standard notebook, calculates the 3D coordinates of all targeted points. The calculation is based on the principle of spatial image triangulation (photogrammetry) and is processed fully automatically. Pre-calibration of the camera is not necessary because the software employs an integrated simultaneous calibration procedure.
DPA Technology
The heart of the measuring systems is the Digital Photogrammetric Analysis (DPA). It allows for completely automated processing of digital images independent of the recording device. The software is easily adaptable to any kind of measuring tasks. In addition to 3D coordinates, DPA provides statistical analysis of the results with specific accuracy information about every coordinate. This allows for instant evaluation of the quality of the measurement.
Benefits in case of 3D inspection of parts
The traditional inspection of parts often requires their transport to a CMM. This is time-consuming and often results in a delay in the availability of the results. The DPA systems offer the capability of conducting the inspection of sheet metal and other parts onsite. This not only saves time and money but also allows for immediate process modifications if required. Fast and automatic analysis of data and production of the final report increases manufacturing reliability and makes quality controls possible at any time without elaborate preparation. DPA is integrated with many measurement software packages, thus allowing for highly automated measuring processes, from processing the photo of the targeted object to the generation of final reports. Software packages that DPA is designed to work with include PolyWorks, RapidForm, Geomagic and others.
Benefits in case of 3D process analysis
In order to shorten the development cycles of increasingly complex parts, it is necessary to collect product dimensional quality information quickly and easily. DPA meets these requirements by providing effortless onsite data analysis. The results can then be directly integrated into the product development process. Moreover, DPA provides dense high quality information. This data allows for the fast and precise evaluation of the dimensional quality of a part, thereby contributing to a reduction in development time.
Request More Information | Product Brochure |